 |
|
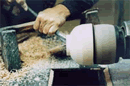 |
|
|
The base wood is first roughly
shaped, then dried thoroughly and turned on a lathe. |
|
 |
|
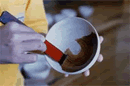 |
|
|
The base wood is first roughly
shaped, then dried thoroughly and turned on a lathe. |
|
 |
|
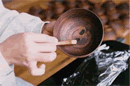 |
|
|
Putty is applied to prevent
damage resulting from imperfections in the base and to smooth the
surface. The imperfections have been scraped out before the surface
preparation stage. The putty, made from a mixture of Japanese paper,
sawdust and lacquer, is applied to even out the irregularities, and
rubbed flat. |
|
 |
|
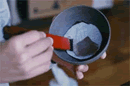 |
|
|
Fabric or paper is used
to reinforce the rim and to counter shrinkage. The threads are arranged
to make an even surface. Areas of overlap are removed and rubbed smooth
after drying. |
|
 |
|
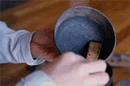 |
|
|
A foundation layer of clay
or powdered stone mixed with lacquer is applied with a wooden spatula
to strengthen and even the surface. Coarse layers are applied, dried
and rubbed down, and the process repeated with successively finer
layers to achieve a smooth surface. For some pieces other materials
are used instead of lacquer, such as glue or persimmon tannin. |
|
 |
|
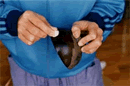 |
|
|
Lacquer is rubbed into the
foundation surface to reinforce it. |
|
 |
|
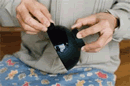 |
|
|
Lacquer is applied with
a brush and dried well. The surface is then scoured to assist the
adhesion of the next layer of lacquer. |
|
 |
|
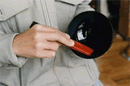 |
|
|
A further coating of lacquer
is applied and left to dry, then rubbed until smooth and free of all
imperfections. This process is to improve the finish of the final
layer of lacquer. |
|
 |
|
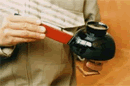 |
|
|
The intermediate lacquer
coating is wiped clean, and a utensil (tsuku) is used to hold
the piece, to prevent fingers from touching the surface and leaving
any body oil, while the final coating of lacquer is applied. (The
tsuku can be seen in the photograph. Great care is taken to
ensure no dirt or unevenness mars the final coating. This is the final
step in the process for some pieces, while others undergo further
polishing). |
|
|